هدف از مواد پوشش دهنده
پوشش سطح خارجی لولههای فولادی برای جلوگیری از زنگزدگی بسیار مهم است. زنگزدگی روی سطح لولههای فولادی میتواند به طور قابل توجهی بر عملکرد، کیفیت و ظاهر بصری آنها تأثیر بگذارد. از این رو، فرآیند پوشش تأثیر قابل توجهی بر کیفیت کلی محصولات لوله فولادی دارد.
-
الزامات مواد پوشش
طبق استانداردهای تعیینشده توسط موسسه نفت آمریکا، لولههای فولادی باید حداقل سه ماه در برابر خوردگی مقاومت کنند. با این حال، تقاضا برای دورههای طولانیتر ضد زنگ افزایش یافته است، به طوری که بسیاری از کاربران به مقاومت ۳ تا ۶ ماهه در شرایط نگهداری در فضای باز نیاز دارند. جدا از نیاز به طول عمر، کاربران انتظار دارند که پوششها سطح صافی را حفظ کنند و عوامل ضد خوردگی را به طور یکنواخت و بدون هیچ گونه پرش یا چکهای که ممکن است بر کیفیت بصری تأثیر بگذارد، توزیع کنند.
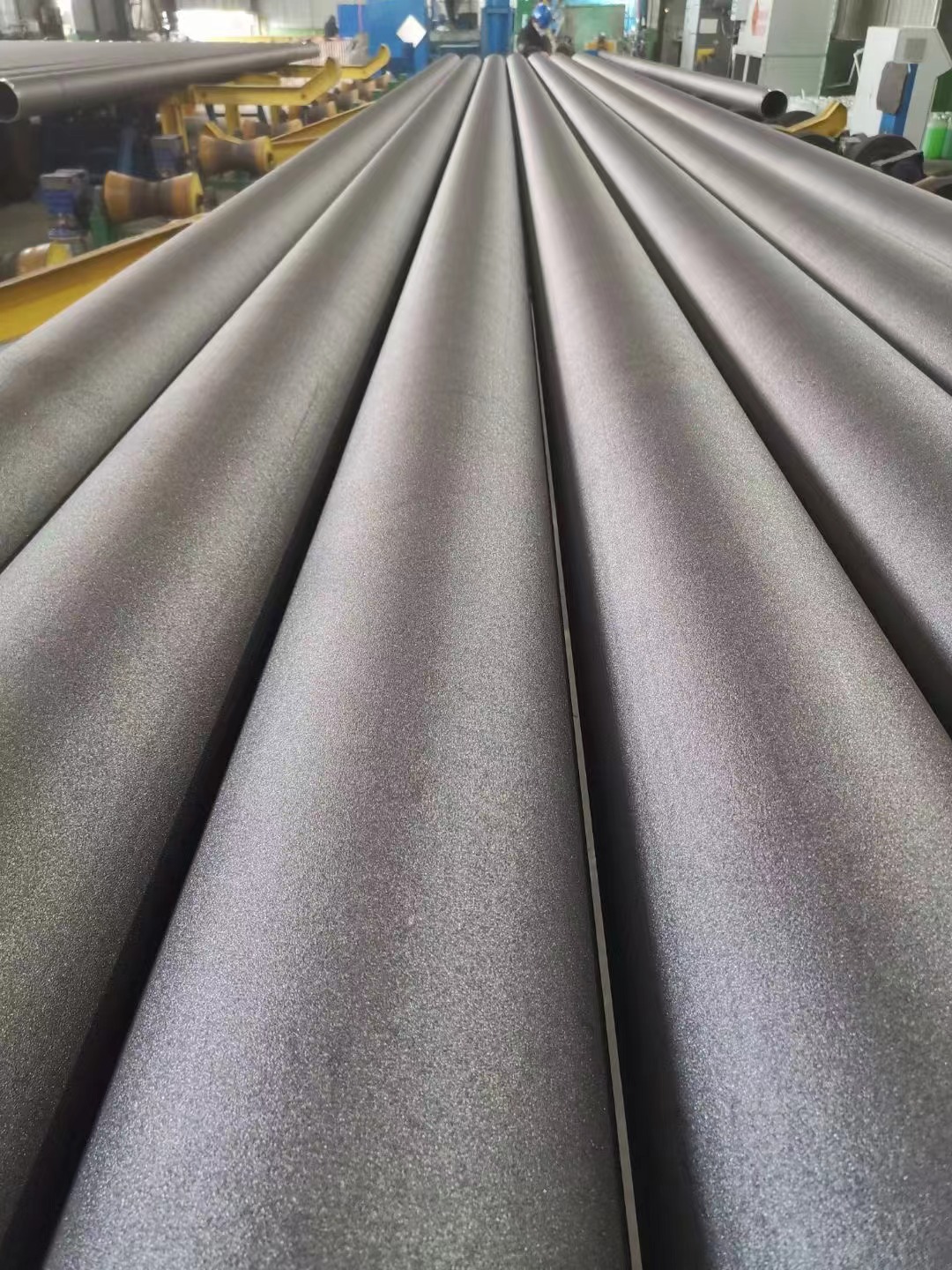
-
انواع مواد پوشش و مزایا و معایب آنها
در شبکههای لولهکشی زیرزمینی شهری،لوله های فولادیبه طور فزایندهای برای انتقال گاز، نفت، آب و موارد دیگر استفاده میشوند. پوششهای این لولهها از مواد آسفالت سنتی به رزین پلیاتیلن و رزین اپوکسی تکامل یافتهاند. استفاده از پوششهای رزین پلیاتیلن از دهه ۱۹۸۰ آغاز شد و با کاربردهای مختلف، اجزا و فرآیندهای پوششدهی به تدریج بهبود یافتهاند.
۳.۱ پوشش آسفالت نفتی
پوشش آسفالت نفتی، یک لایه ضد خوردگی سنتی، از لایههای آسفالت نفتی، تقویت شده با پارچه فایبرگلاس و یک فیلم محافظ خارجی پلی وینیل کلرید تشکیل شده است. این پوشش ضد آب بودن عالی، چسبندگی خوب به سطوح مختلف و مقرون به صرفه بودن را ارائه میدهد. با این حال، دارای معایبی از جمله حساسیت به تغییرات دما، شکننده شدن در دماهای پایین و مستعد پیری و ترک خوردگی، به ویژه در شرایط خاک سنگی است که نیاز به اقدامات حفاظتی اضافی و افزایش هزینهها را ایجاب میکند.
۳.۲ پوشش اپوکسی قطران زغال سنگ
اپوکسی قطران زغال سنگ، ساخته شده از رزین اپوکسی و آسفالت قطران زغال سنگ، مقاومت عالی در برابر آب و مواد شیمیایی، مقاومت در برابر خوردگی، چسبندگی خوب، استحکام مکانیکی و خواص عایق را نشان میدهد. با این حال، پس از اعمال به زمان پخت طولانیتری نیاز دارد و در این دوره مستعد اثرات نامطلوب شرایط آب و هوایی است. علاوه بر این، اجزای مختلف مورد استفاده در این سیستم پوششی نیاز به نگهداری تخصصی دارند که هزینهها را افزایش میدهد.
۳.۳ پوشش پودری اپوکسی
پوشش پودری اپوکسی که در دهه 1960 معرفی شد، شامل پاشش پودر به صورت الکترواستاتیکی روی سطوح لوله از پیش آمادهسازی شده و از پیش گرم شده است که یک لایه متراکم ضد خوردگی تشکیل میدهد. مزایای آن شامل طیف وسیعی از دما (-60 درجه سانتیگراد تا 100 درجه سانتیگراد)، چسبندگی قوی، مقاومت خوب در برابر جدایش کاتدی، ضربه، انعطافپذیری و آسیب جوش است. با این حال، لایه نازکتر آن، آن را مستعد آسیب میکند و به تکنیکها و تجهیزات تولید پیچیدهای نیاز دارد که چالشهایی را در کاربرد میدانی ایجاد میکند. اگرچه از بسیاری جهات برتری دارد، اما از نظر مقاومت در برابر حرارت و محافظت کلی در برابر خوردگی در مقایسه با پلیاتیلن کم میآورد.
۳.۴ پوشش ضد خوردگی پلی اتیلن
پلیاتیلن مقاومت ضربهای عالی و سختی بالایی را در کنار محدوده دمایی وسیع ارائه میدهد. به دلیل انعطافپذیری و مقاومت ضربهای برتر، به ویژه در دماهای پایین، در مناطق سردسیر مانند روسیه و اروپای غربی برای خطوط لوله کاربرد گستردهای دارد. با این حال، چالشهایی در کاربرد آن در لولههای با قطر بزرگ وجود دارد، جایی که ممکن است ترک خوردگی ناشی از تنش رخ دهد و ورود آب میتواند منجر به خوردگی در زیر پوشش شود، که مستلزم تحقیقات بیشتر و بهبود در مواد و تکنیکهای کاربرد است.
۳.۵ پوشش ضد خوردگی قوی
پوششهای ضد خوردگی سنگین در مقایسه با پوششهای استاندارد، مقاومت به خوردگی قابل توجهی را ارائه میدهند. آنها حتی در شرایط سخت، اثربخشی طولانیمدتی را نشان میدهند و طول عمر آنها در محیطهای شیمیایی، دریایی و حلالها بیش از 10 تا 15 سال و در شرایط اسیدی، قلیایی یا نمکی بیش از 5 سال است. این پوششها معمولاً ضخامت لایه خشک از 200 میکرومتر تا 2000 میکرومتر دارند که محافظت و دوام عالی را تضمین میکند. آنها به طور گسترده در سازههای دریایی، تجهیزات شیمیایی، مخازن ذخیرهسازی و خطوط لوله استفاده میشوند.
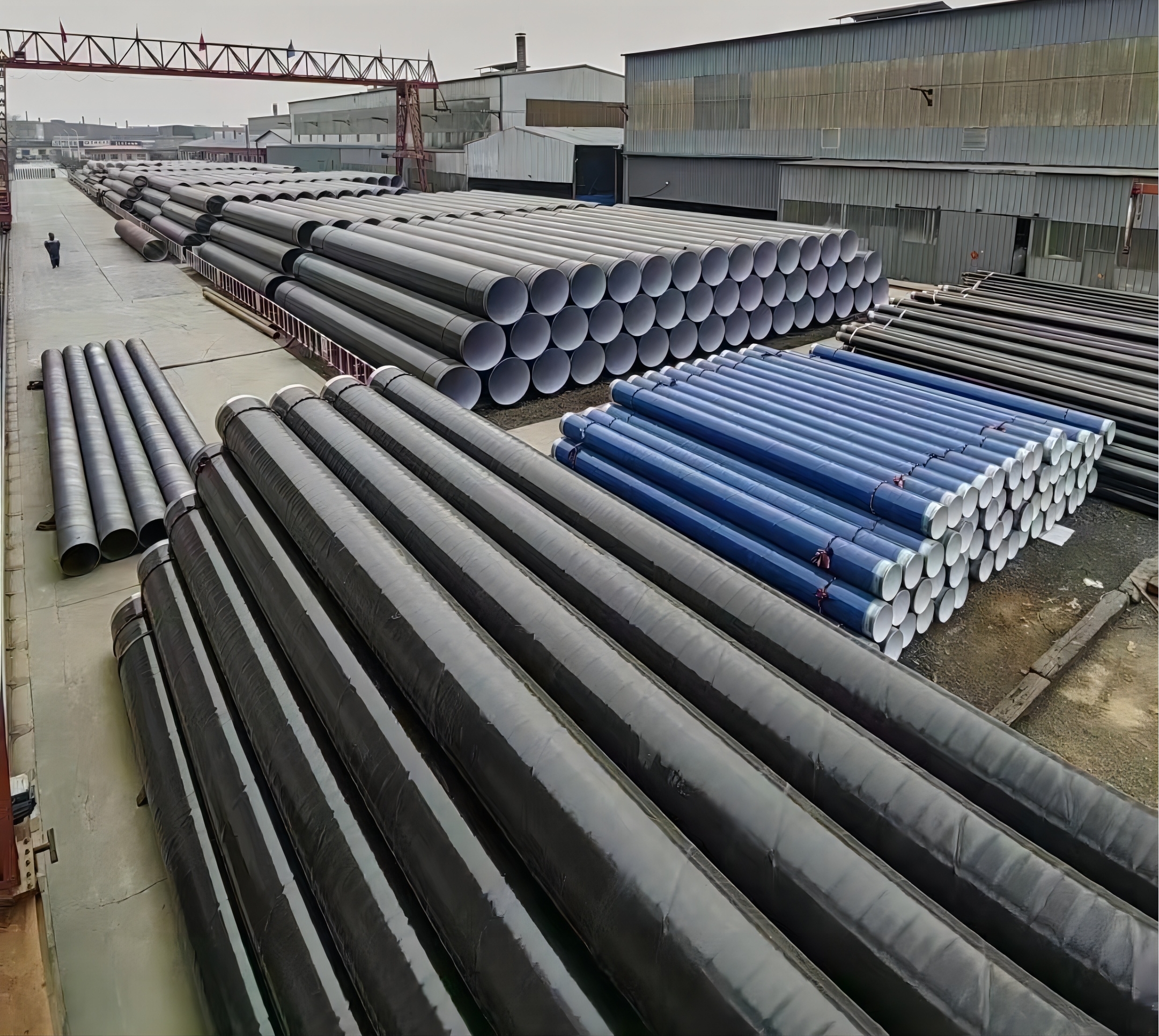
-
مشکلات رایج با مواد پوششی
مشکلات رایج در مورد پوششها شامل کاربرد ناهموار، چکه کردن مواد ضد خوردگی و تشکیل حباب است.
(1) پوشش ناهموار: توزیع ناهموار عوامل ضد خوردگی روی سطح لوله منجر به ایجاد مناطقی با ضخامت پوشش بیش از حد میشود که منجر به هدر رفتن میشود، در حالی که مناطق نازک یا بدون پوشش، قابلیت ضد خوردگی لوله را کاهش میدهند.
(2) چکیدن مواد ضد خوردگی: این پدیده، که در آن مواد ضد خوردگی به صورت قطراتی روی سطح لوله جامد میشوند، بر زیباییشناسی تأثیر میگذارد، در حالی که مستقیماً بر مقاومت در برابر خوردگی تأثیر نمیگذارد.
(3) تشکیل حباب: هوای محبوس شده در داخل ماده ضد خوردگی در حین استفاده، حبابهایی را روی سطح لوله ایجاد میکند که هم بر ظاهر و هم بر اثربخشی پوشش تأثیر میگذارد.
-
تحلیل مسائل مربوط به کیفیت پوشش
هر مشکلی از دلایل مختلفی ناشی میشود و توسط عوامل مختلفی ایجاد میشود؛ و یک دسته لوله فولادی که با کیفیت مشکل برجسته میشود، ممکن است ترکیبی از چندین مورد نیز باشد. علل پوشش ناهموار را میتوان تقریباً به دو نوع تقسیم کرد، یکی پدیده ناهمواری است که در اثر پاشش پس از ورود لوله فولادی به جعبه پوشش ایجاد میشود؛ دوم پدیده ناهمواری است که در اثر عدم پاشش ایجاد میشود.
دلیل پدیده اول به وضوح قابل مشاهده است، زیرا وقتی لوله فولادی با زاویه ۳۶۰ درجه وارد جعبه پوشش میشود، در مجموع ۶ تفنگ (خط لوله پوششی ۱۲ تفنگ دارد) برای پاشش وجود دارد. اگر اندازه جریان پاشش شده در هر تفنگ متفاوت باشد، منجر به توزیع ناهموار ماده ضد خوردگی در سطوح مختلف لوله فولادی خواهد شد.
دلیل دوم این است که علاوه بر عامل پاشش، دلایل دیگری نیز برای پدیده پوشش ناهموار وجود دارد. عوامل مختلفی مانند زنگ زدگی لوله فولادی، زبری سطح وجود دارد که توزیع یکنواخت پوشش را دشوار میکند؛ سطح لوله فولادی هنگام تماس امولسیون با امولسیون، فشار آب را به جا میگذارد، به طوری که اتصال ماده نگهدارنده به سطح لوله فولادی دشوار است، به طوری که هیچ پوششی روی قطعات لوله فولادی توسط امولسیون وجود ندارد و در نتیجه پوشش کل لوله فولادی یکنواخت نیست.
(1) دلیل معلق ماندن قطرات عامل ضد خوردگی. سطح مقطع لوله فولادی گرد است، هر بار که عامل ضد خوردگی روی سطح لوله فولادی اسپری میشود، عامل ضد خوردگی در قسمت بالایی و لبه به دلیل عامل گرانش به قسمت پایینی جریان مییابد که پدیده معلق ماندن قطرات را تشکیل میدهد. نکته خوب این است که در خط تولید پوشش کارخانه لوله فولادی، تجهیزات کوره وجود دارد که میتواند عامل ضد خوردگی اسپری شده روی سطح لوله فولادی را به موقع گرم و جامد کند و سیالیت عامل ضد خوردگی را کاهش دهد. با این حال، اگر ویسکوزیته عامل ضد خوردگی زیاد نباشد؛ پس از اسپری به موقع گرم نشود؛ یا دمای گرمایش زیاد نباشد؛ نازل در شرایط کاری خوبی نباشد و غیره، منجر به معلق ماندن قطرات عامل ضد خوردگی میشود.
(2) علل کف کردن ضد خوردگی. با توجه به رطوبت هوا در محیط عملیاتی، پراکندگی رنگ بیش از حد است و افت دمای فرآیند پراکندگی باعث ایجاد پدیده حباب زدن مواد نگهدارنده میشود. در محیط مرطوب، شرایط دمایی پایینتر، مواد نگهدارنده به قطرات ریز پراکنده شده و منجر به افت دما میشوند. آب موجود در هوا با رطوبت بالاتر پس از افت دما، متراکم شده و قطرات ریز آب را تشکیل میدهد که با مواد نگهدارنده مخلوط شده و در نهایت وارد پوشش میشوند و در نتیجه پدیده تاول زدن پوشش ایجاد میشود.
زمان ارسال: ۱۵ دسامبر ۲۰۲۳